Bonding Untreated Thermoplastic Polyolefin
- GlueOnline
- Permabond at GlueOnline
- 17 May 2023
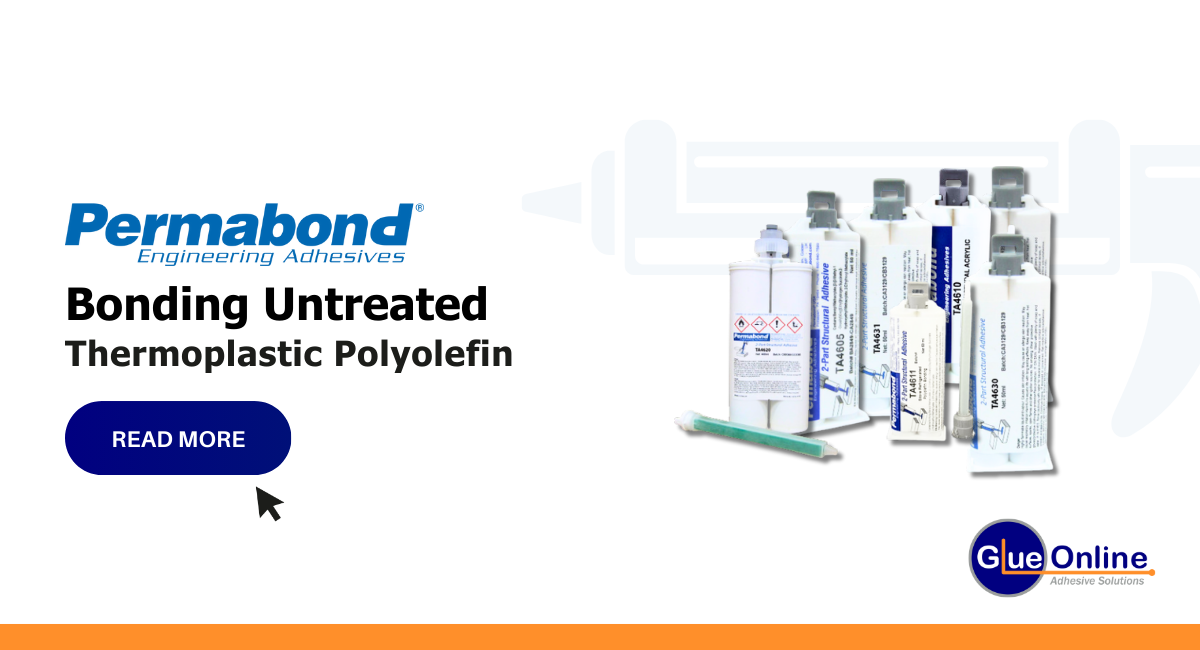
Bonding Untreated Thermoplastic Polyolefin
Bonding thermoplastic polyolefins such as polypropylene and polyethylene can be challenging due to their low surface energy and chemical structure. Technical issues can arise when trying to bond these materials such as:
- Poor wetting: polyolefins have low surface energies, which makes it difficult for adhesives or coatings to wet out and adhere to their surfaces. This results in weak adhesion and poor bonding
- Chemical resistance: polyolefins are highly resistant to chemical attacks, which makes it difficult for many adhesives and coatings to create a strong bond.
- Thermal expansion: polyolefins have a relatively high coefficient of thermal expansion, meaning that they expand and contract significantly with changes in temperature. This can cause stress on the bond line, leading to bond failure over time.
- Creep: polyolefins exhibit creep, which means they slowly deform under stress over time. This can lead to a loss of contact and subsequent bond failure.
To overcome these, pre-treatment methods such as flame or corona treatment or surface activation are normally required.
Challenges with Polyolefin Surface and Pre-Treatments
While flame or corona treatment and surface activation can improve the bonding of polyolefins, there are still some issues to be aware of:
- Short-lived effects: The surface activation methods provide only temporary surface energy to the material; this means that the bond strength may decrease over time if not used in combination with an appropriate adhesive.
- Surface contamination: During manufacturing, polypropylene and polyethylene may accumulate contaminants on their surfaces, such as oil or mould release agents. These contaminants can affect the effectiveness of the surface treatment, leading to poor adhesion.
- Complex processing: Surface activation methods can be complex and require specialised equipment and expertise. This can make the manufacturing process more expensive and time-consuming.
- Material compatibility: The effectiveness of surface activation methods can vary depending on the type of polypropylene or polyethylene used, and the specific adhesive or coating used.
- Safety concerns: Flame or corona treatment can involve high temperatures or electrical discharge, which can pose safety risks if not handled correctly.
- Environmental concerns: Surface activation methods may involve the use of chemicals or solvents that can be harmful to the environment. So while surface activation methods can be effective for improving the bonding of polypropylene and polyethylene, they should be carefully considered for their safety and environmental impact.
Permabond ® TA46** Structural Acrylics Bond Untreated Polyolefins
The Permabond TA46** range was developed to bond untreated polyolefin surfaces. These adhesives are ideal for bonding polypropylene and polyethylene – without the need to carry out costly surface pre-treatment before bonding. They can also be used to bond polyolefin to a wide variety of other substrate materials, including composites, e-coatings, EPDM, HDPE, LPDE, most metals, PTFE and UHMW. All offer full cure at room temperature come in a easy to use 1:1 mix ratio, allowing them to be applied manually or using automatic dispensing equipment.
There are 6 grades in the TA46** range, each with its own unique feature
- TA4605 featuring fast cure with working strength in 2 – 4 hours
- TA4610 which offers fast curing for larger components
- TA4611 for smaller gap fill (no micro beads)
- TA4620 slow cure for large surface areas
- TA4630 low odour, with microbeads
- TA4631 low odour, smaller gap fill (no micro beads)
For further information on product specifications or to request technical datasheets contact our team directly.
How to Use Permabond TA46** Range to Bond Polyolefin Surface
- Surfaces must be clean, dry and grease-free prior to bonding.
- Apply a thin bead of adhesive pre-mixed through a static mixer nozzle.
- Assemble components and clamp.
- Maintain pressure until handling strength is achieved. The time required will vary according to the joint design and surfaces being bonded.
- Allow 24 hours for adhesive to fully cure. Note adhesive outside of a closed joint (i.e. excess material) will cure more slowly and may be soft due to air contact. Adhesive inside the joint will cure solid.
Shop Online